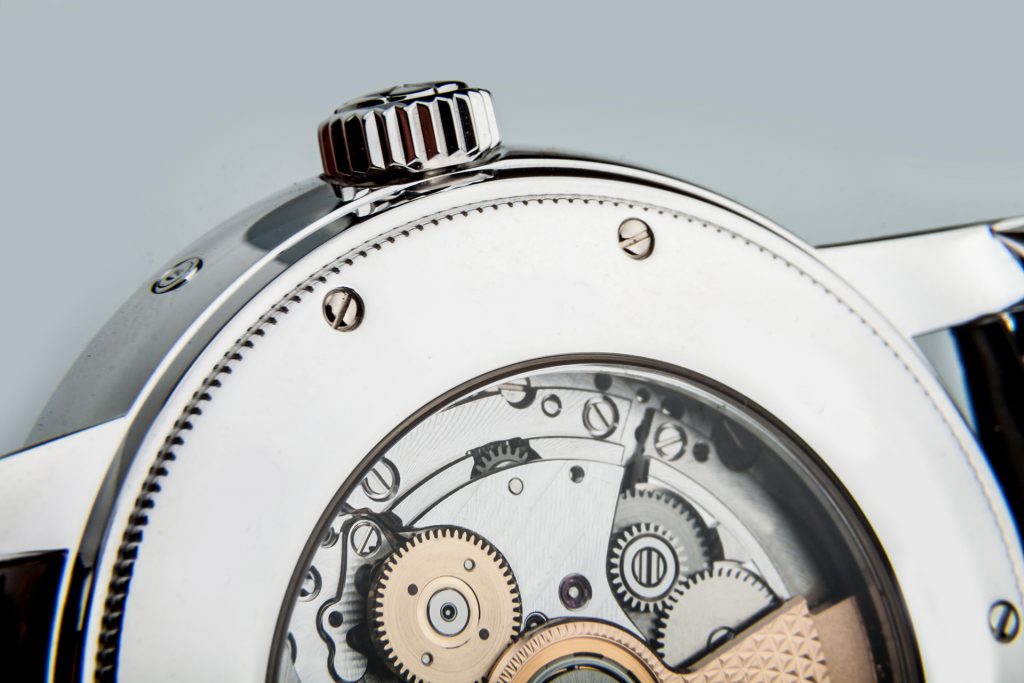
Although essential, know-how isn’t everything.
From elements, men and machines, your know-how creates this magic, helping to maintain the quality of Swiss watchmaking.
Nonetheless, the agile cohabitation of different strategic areas of the company, with the aim of creating value, remains a challenge for all manufacturing companies, if they wish to maintain a constant level of quality.
Dynamics Business Excellence SA can help you set up easily understandable and efficient processes through ERP Microsoft Dynamics NAV.
Fully integrated into the Microsoft ecosystem, the solution Dynamics NAV you will provide you with a global vision of your business, while guaranteeing effective supply chain management and optimal control of your production environment. Having the information you need to make the right decisions at the right time will be the key to your success.
What’s in it for me NAV in a real-life situation?
It’s no secret that today’s market is increasingly difficult and demand extremely volatile. A company’s aim is to achieve customer service levels as close to 100% as possible. But keeping stock levels high will incur costs, while keeping them low can lead to logistical complications. So it’s hard to find the right balance without a management tool.
A production manager will therefore need to find the right balance and combination for optimum results at minimum cost. One of the keys to achieving an ideal result is the use of a production management tool integrating a reliable forecasting system and efficient, relevant planning. This will enable requirements from the sales department to be scheduled and passed on to the inventory, purchasing and workshop departments.
In order to fulfil his production planning and management mission efficiently, he will have to define production bills of materials and operating procedures, in coordination with the design and methods department, while providing the quality control plan needed to validate production. These same two departments will have worked with the management department to validate the most advantageous standard production cost for the company, while integrating the costs of manufacturing semi-finished products by subcontractors.
Once these elements have been implemented, planning and scheduling can be launched. Validation of the scheduled proposals enables production orders to be created for the workshops, accompanied by production follow-up sheets. The warehouse receives the list of components or semi-finished products to be destocked for the production line. The purchasing department receives orders for components and/or subcontractors.
Inventory management traceability & after-sales service.
Inventory management is an essential part of managing the needs of any business. This is even truer when the company is producing. A single missing item can bring the entire production chain to a standstill. However, having stock comes at a considerable cost. You can count on the possibilities of parameterization by Microsoft Dynamics NAV to define stock management and replenishment rules for each item. In this way, based on forecasts of the use of each component, you can secure your costs by avoiding out-of-stock situations.
The traceability of certain components and/or finished luxury products remains a guarantee of seriousness and quality for the end customer, who has access to an exceptional item. Its product is unique by its serial number. Microsoft Dynamics NAV enables you to trace a component’s batch and/or serial number back to the final product.
In the same way, using a serial number for a final product, the traceability of all components used in the manufacture of the item can be consulted via an easy-to-use matrix. While the end customer can be sure of having a product that is unique by virtue of its serial number, the manufacturer, thanks to this serial number and the after-sales management module, can track the entire life of the product and the associated interventions.
En effet Microsoft Dynamics NAV offers the possibility of creating a unique service item for each product sold. From this service item, it will be possible to carry out after-sales interventions, which may or may not be invoiced if the item is under warranty.
Comments are closed.